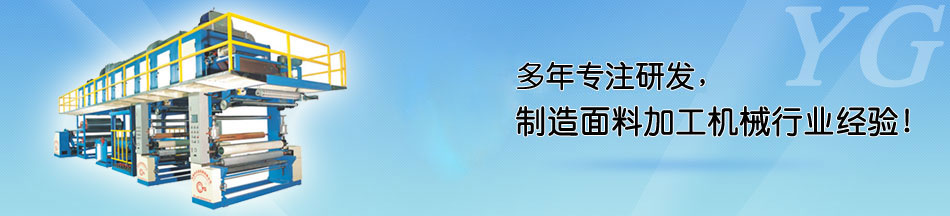
在復(fù)合機(jī)的生產(chǎn)過程中,常常會遇到氣泡、起皺、粘結(jié)不主等缺陷,這些缺陷不僅影響產(chǎn)品的外觀質(zhì)量,還可能對產(chǎn)品的使用性能造成嚴(yán)重影響。本文將針對這些常見缺陷,提出相應(yīng)的解決方法。
一、避免成品產(chǎn)出氣泡的方法
1、膠黏劑選擇不當(dāng)
解決方法:選用與基材相匹配的膠黏劑,并根據(jù)復(fù)合膜的最終用途選擇適當(dāng)?shù)哪z黏劑類型,如耐高溫蒸煮型膠黏劑、抗酸辣鋁箔專用膠黏劑等。
2、涂膠量不足
解決方法:提高涂膠量,可以通過選用網(wǎng)穴較深的網(wǎng)紋、增大橡膠輥壓力、減少刮刀與網(wǎng)紋輥的接觸壓力等方式來實(shí)現(xiàn)。
3、基材電暈處理
有些基材表面黏附膠黏劑的能力差,為了提高這類基材表面的黏附能力,保證涂布質(zhì)量,要求基材的表面張力要達(dá)到42~56Mn/cm左右,可以在涂布前增加一套電暈處理器對基材表面進(jìn)行電暈處理,使表面起毛,以達(dá)到增強(qiáng)表面張力的作用,這樣就能提高基材表面的涂膠量以避免氣泡產(chǎn)生。
4、合適的烘干溫度
烘干溫度合適,可以使基材表面的膠黏劑充分干燥,一般干澡溫度調(diào)節(jié)至80~100℃為宜,若溫度過高,膠黏劑表面已經(jīng)結(jié)皮,表面以下的部分還未干透,使廢氣難以逸出,就容易出現(xiàn)起泡。
相反,溫度太低,膠黏劑無法徹底干燥,經(jīng)過了一段時間復(fù)合后的成品,由于膠黏劑自然揮發(fā),也會形成氣泡,復(fù)合時提高復(fù)合加熱輥的溫度,減小復(fù)合角度,有利于氣泡排出。
5、調(diào)節(jié)復(fù)合壓力與速度
復(fù)合壓力不夠,容易產(chǎn)生氣泡,提高復(fù)合膜的壓合溫度和復(fù)合壓力,就能大大減少氣泡。由于兩個復(fù)合輥的接觸為線拉觸,所以降低設(shè)備的運(yùn)行速度就可以增加復(fù)合輥間的壓貼時間,使氣泡充分從復(fù)合膜中排出,也有利于減少氣泡。
另外,為防灰塵黏附后在薄膜的復(fù)合表面上,需要清潔網(wǎng)紋輥和薄膜,清洗復(fù)合輥,注意環(huán)境衛(wèi)生。
二、避免貼合機(jī)起皺的方法
1、基材張力過大
解決方法:適當(dāng)降低基材的張力,防止薄膜拉伸過大導(dǎo)致冷卻收縮時起皺。
2、導(dǎo)輥不平行
解決方法:調(diào)整導(dǎo)輥的平行度,確?;脑趯?dǎo)輥上能夠平穩(wěn)運(yùn)行。
3、復(fù)合壓力不均
解決方法:調(diào)節(jié)復(fù)合輥的壓力,使其均勻分布,避免復(fù)合膜表面出現(xiàn)皺褶。
4、收卷張力不合適
解決方法:調(diào)節(jié)收卷張力,確保收卷后的復(fù)合膜平整無皺。
三、牢結(jié)不牢的問題
1、膠黏劑選擇不當(dāng)
解決方法:選用與基材和復(fù)合膜最終用途相匹配的膠黏劑,確保膠黏劑的性能能夠滿足使用要求
2、涂膠量不足
解決方法:提高涂膠量,確保膠黏劑能夠均勻覆蓋基材表面形成良好的粘結(jié)效果。
3、烘干溫度不合適
解決方法:調(diào)節(jié)烘干溫度,確保膠黏劑能夠充分固化,同時避免溫度過高導(dǎo)致膠黏劑炭化破壞粘結(jié)能力。
4、復(fù)臺壓力不足或不均
解決方法:適當(dāng)增加復(fù)合壓力,并確保復(fù)合兩端的壓力均勻分布,提高復(fù)合膜的粘結(jié)牢度。
5、基材表面特性不佳
解決方法:對基材進(jìn)行充分的表面處理,如清潔、除塵、提高表面濕潤性等,以提高其與膠黏劑的粘結(jié)能力。
綜上所述,針對復(fù)合生產(chǎn)中的氣泡、起皺、粘結(jié)不牢等缺陷,可以從膠黏劑選擇、涂膠量控制、烘干溫度調(diào)節(jié)、復(fù)合壓力調(diào)整、基材表面處理以及設(shè)備維護(hù)等方面入手,采取相應(yīng)的解決方法,確保復(fù)合的生產(chǎn)質(zhì)量。